Packaging plays a crucial role in capturing consumers' attention, persuading them to purchase products, and serving as a medium for brand communication. A well-designed packaging stands out from the crowd and leaves a positive impression on consumers' minds. Consumers often perceive a brand's quality based on various design elements of the packaging. Shape, color, images, text, material, and convenience are essential elements in cosmetics branding, typically incorporated through post-processing during manufacturing. Post-processing generally refers to additional treatments, modifications, or enhancements applied to packaging after the initial manufacturing stage. This phase is vital for achieving specific properties, enhancing aesthetics, improving functionality, or meeting regulatory standards. There are several common post-processing techniques for packaging, including:
1. Color injection
Color injection is a process to incorporate color additives directly into the material resin during manufacturing, allowing for a choice of expected colors based on Pantone colors, with options for transparency adjustment, solid colors, or gradations.
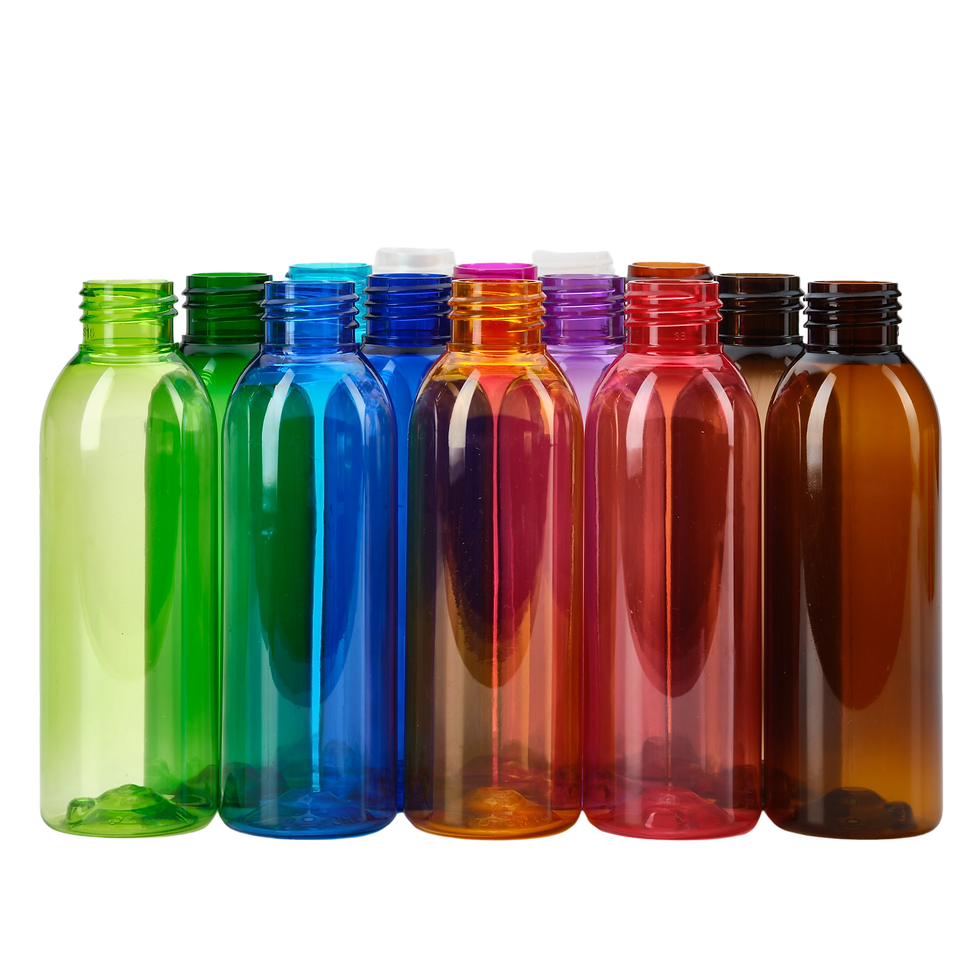

2. Printing
Printing is a process to add information, branding, or decorative elements through ink printing methods such as screen printing (silk printing), heat transfer printing, and 3D printing.
a. Silk printing involves allowing ink to flow into a designated pattern on a printing screen, similar to printing on a T-shirt. It's the most common method for printing on flat or curved surfaces of plastic containers, applying one color at a time.
b. Heat transfer printing applies graphics or images from a carrier (often special paper or film) onto packaging using heat and pressure, much like applying a tattoo sticker. This method allows for printing multiple colors simultaneously.
c. 3D printing creates logos, patterns, and images on packaging to give them a three-dimensional effect
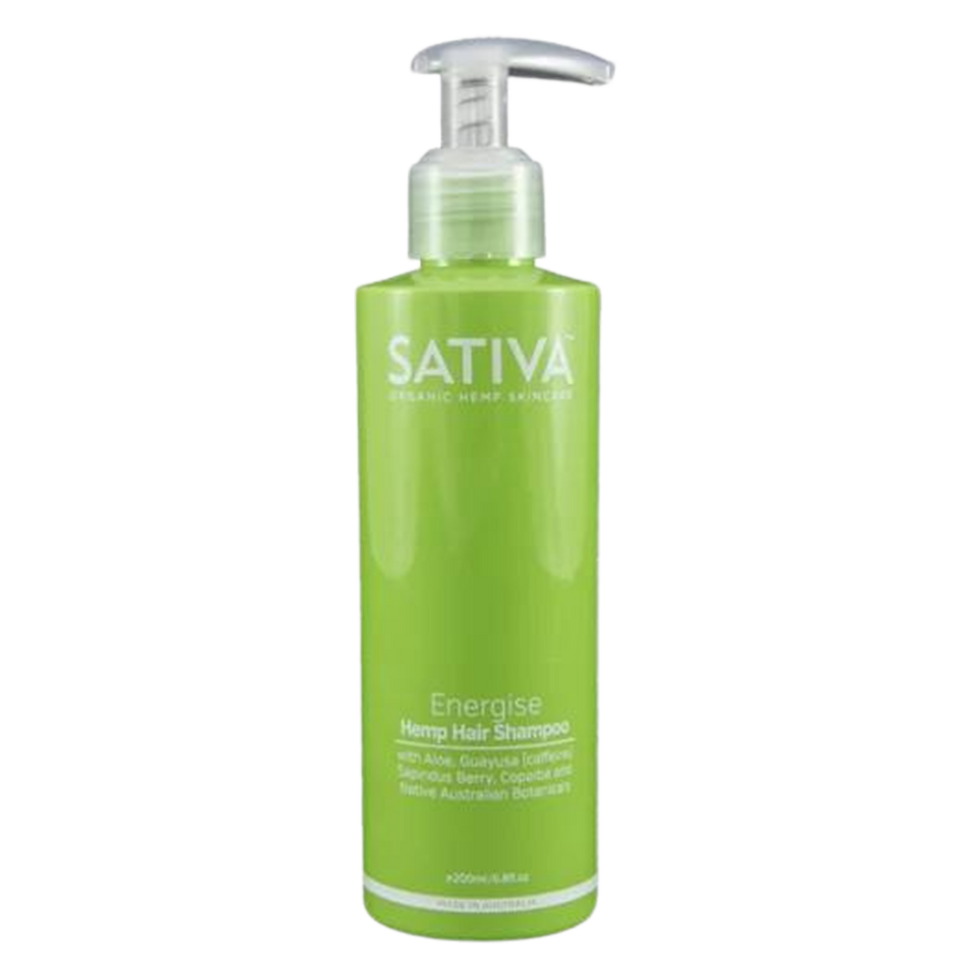


3. Labelling
Labelling is a process to attach labels or stickers containing product information, barcodes, or promotional messages.
.
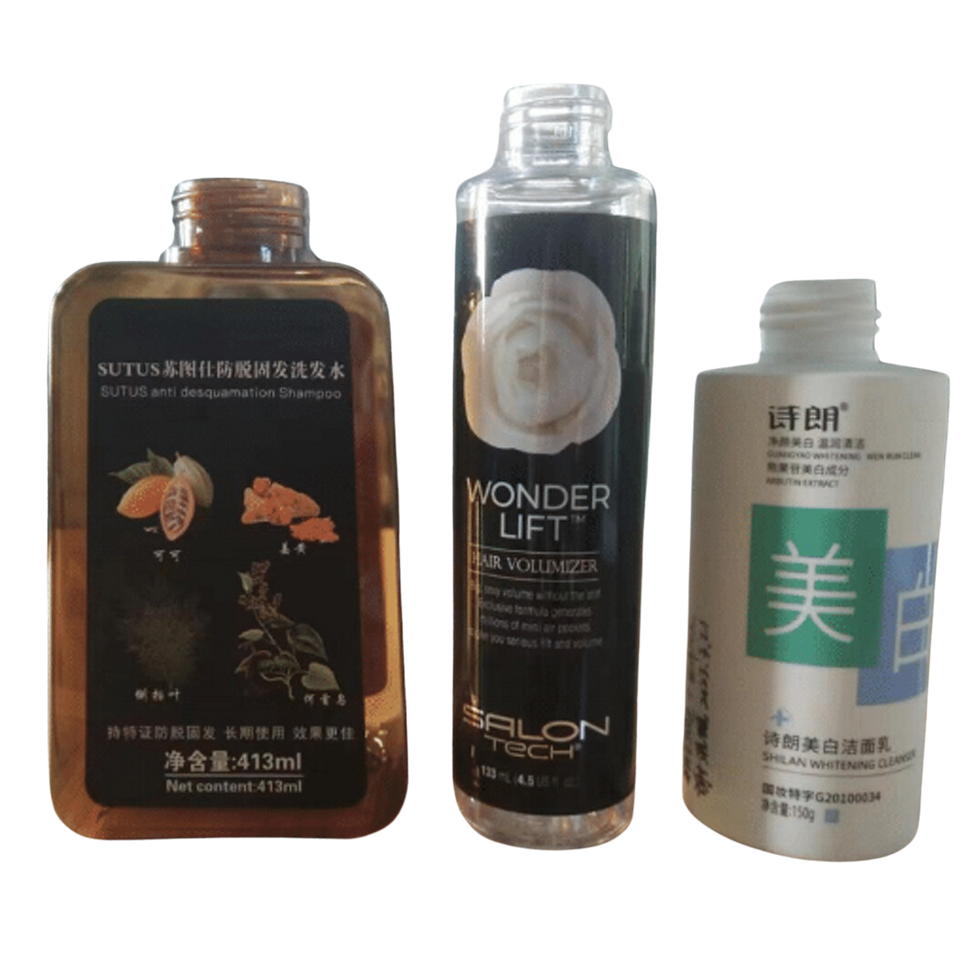
4. Hot stamping
Hot stamping is a procedss to apply colored or metallic foil to a surface using heat and pressure, often used for adding decorative elements, logos, or text.

5. Coating
Coating is a process to apply a layer of material onto the packaging surface for functional, aesthetic, or protective purposes, including glossy, matte, UV, and soft-touch coatings. There are various common coating options utilized in cosmetics packaging as follows.
a. Glossy coating is frequently utilized on packaging to achieve a sleek and reflective surface, enhancing its visual appeal with a polished and upscale appearance.
b. Matte coating offers a non-reflective or velvety texture to packaging, often preferred for its refined and contemporary look.
c. UV coating applies a clear and glossy layer to the packaging surface, amplifying color vibrancy, providing a glossy finish, and offering some level of protection against scratches.



6. Metallization
Metallization is a process to apply a thin layer of metal onto the plastic surface to enhance visual appeal and overall performance.

7. Holographic effect
Holographic effect is a process to use holographic materials or printing techniques to create dynamic and shimmering appearances, characterized by a play of colors and shifting patterns. Holographic effects are often applied to labels, boxes, packaging films, or product containers for a captivating visual experience.

Comments